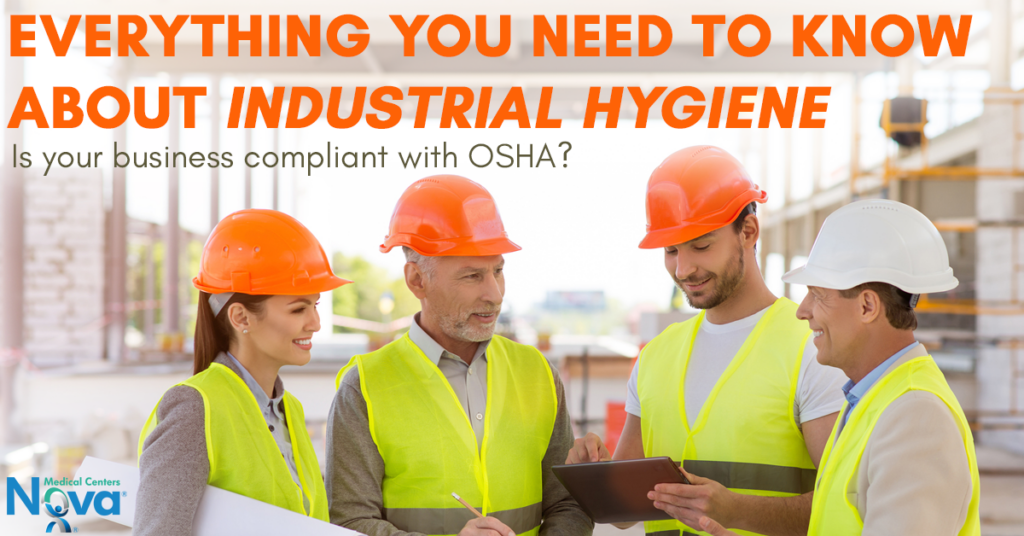
Is your business compliant with OSHA?
According to the Occupational Safety and Health Administration, Industrial Hygiene is defined as the science and art devoted to the anticipation, recognition, evaluation, and control of those environmental factors or stresses arising in or from the workplace, which may cause sickness, impaired health, and well-being, or significant discomfort among workers or among the citizens of the community. It is the responsibility of the employer to make sure that their workplaces are safe not only for their employees but for the community that surrounds them.
The first step in industrial hygiene is to conduct a workplace analysis. OSHA describes a workplace analysis as the essential first step that helps industrial hygienists to determine what jobs and workstations are the sources of potential problems. The analysis can include but is not limited to:
- Interviews with workers
- Inventories of chemical and hazardous materials
- Job task observations
- Reviews of work schedules, production records, accident and incident reports, equipment and maintenance schedules, safety programs, written procedures, and chemical safety data sheets (SDS)
- Performing change analyses
- Job hazard analyses (JHAs)
- Routine worksite inspections
- Creating an effective system for employees to report hazards and near misses
- Performing incident investigations
- Analysis of injury and illness trends over time
Once the hazards have been identified, the next step is for an industrial hygienist to put controls in place to eliminate or reduce the risk of the hazard in the workplace. OSHA lists three different controls that can take place:
- Engineering controls- Either reduce or remove hazards at the source or isolate workers from the hazard.
- Work practice controls- Alter how the task is performed. This can include changing work practices, maintaining equipment, prohibiting food and drinks, etc.
- Administrative controls-Reducing exposure by scheduling production and tasks during the lowest exposure potential hours.
Along with these steps, make sure that your employees are always wearing personal protective equipment in potentially hazardous environments. In order for your workplace to be compliant with OSHA standards, these steps should be implemented in your business to keep your workers healthy and safe. You may also like Personal Protective Equipment: Be Safe Not Sorry and Working in Confined Spaces: What You Need to Know to Stay Safe.